2019 年生态环境部发布《关于推进钢铁行业超低排放的意见》,要求钢铁企业因厂制宜选择成熟适用的环保改造技术,加强源头控制,高炉煤气、焦炉煤气应实施精脱硫。宝山钢铁股份有限公司宝山基地(以下简称宝钢)高度重视,结合厂情特点和已有成果,对尚未达到超低排放的轧钢工序,继续开展了煤气源头脱硫治理的技术研究和工程实践。1 含硫量及脱硫方向分析
1.1 烟气排放现状
根据超低排放要求,每月95%以上时段烟气SO2浓度应<50mg/m³(小时均值,基准含氧量8%),宝钢不满足超低排放的轧钢加热炉窑共39台。虽然烟气排放SO2平均浓度超标不多,但波动从时间序列上波动很大。转换为概率问题,以热轧某排口的近万条数据为例(见图1),95%以上时段合格,意味着该测点烟气SO2浓度最高已达到<95mg/m³。扩展到各排口,烟气SO2浓度最高在<83-99mg/m³,这意味着需要将煤气中的硫脱除一半。
1.2 人工检定煤气含硫量
获知源端各类副产煤气的含硫量,是环保治理及监测的基础条件,是确定工艺方向乃至 工艺设计极为重要的环节。上百组的人工取样煤气全硫组分分析表明(见表1):COG 中 的硫化物以CS2(二硫化碳)、COS(羰基硫)为主,并含有C4H4S(噻吩)、CH3SH(甲硫醇)等少量杂硫;BFG 中硫化物以 COS、H2S 为主;LDG 基本不含硫;COG 总硫含量约接近BFG总硫含量的3 倍。
1.3 烟气反算煤气含硫量
然而,当煤气中硫元素以有机硫形态存在时,检测过程非常复杂,源端煤气的总硫或有机硫在线实时检测困难,数据样本完全不足以覆盖至少 95%以上时段,无法得到前述烟气含硫量 83-99mg/m³,这说明烟气排放高值时的煤气含硫量未检测到。因此,通过其它参数的大数据分析得到源端煤气含硫量,在一定置信区间内实现煤气含硫量的软测量,对于指导脱硫系统的设计和脱硫系统运行具有重要价值。这个基本思路如图2所示。经过数据比对,正算的烟气SO2浓度与实测到的烟气SO2浓度误差在 1%~7%;由烟气SO2浓度反向计算煤气含硫量,在相同时段与对煤气的实际测量值接近。说明正算结合反算的计算分析方法合理有效,可以进行大数据分析。当然,烟气和煤气数据来自不同的系统,数十万条数据需要先经过预处理,包括对齐时间、剔除检测数据异常点、剔除年修等。表2给出了计算某小时煤气含硫量各步骤的结果。①因LDG 基本不含硫,先选取混烧BFG+LDG 的高炉热风炉烟气数据,计算得到 BFG 含硫量;②选取混烧BFG+COG的厚板1#加热炉烟气数据,结合前述得到的 BFG 含硫量,计算得到COG 的含硫量。基本方法是:①根据烟气中O2含量推算过剩空气系数;②结合烟气SO2数据得到煤气含硫量;③根据煤气比例得到单种煤气含硫量。如此对各加热炉烟气排口数据逐时计算,汇总为COG 总硫的数据集,得出COG总硫的平均值,以及覆盖95%时段的COG总硫最高值(列于表3),可见烟气反算出的COG。含硫量相较表1的人工取样检测,波动范围是比较大的,平均值约420mg/m³(以SO2计),最大值可接近900mg/m³(以SO2计),该最大值即为精脱硫系统设计条件。另外,由烟气反算出的 BFG 含硫量与人工取样平均值接近,最大值约 180mg/m³(以SO2计)。
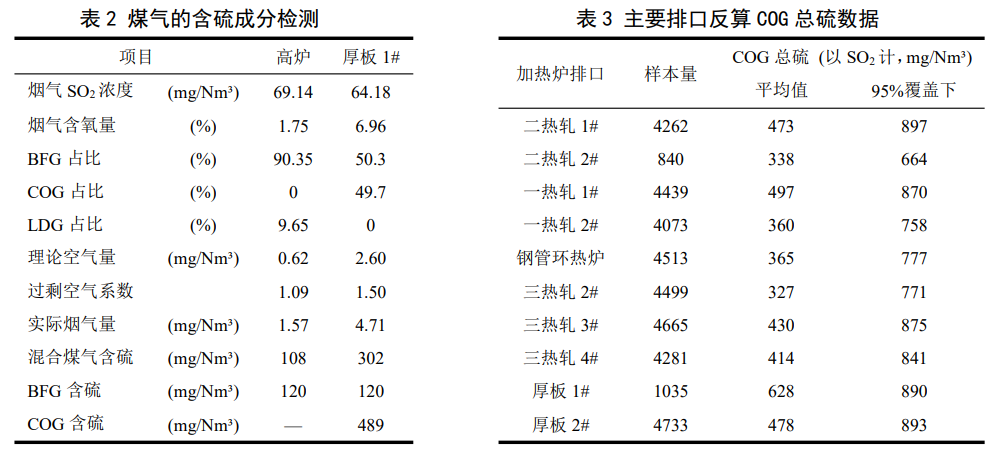
1.4 煤气精脱硫方向
轧钢工序典型燃料结构为:39%BFG+40%COG+20%LDG(30台),52%BFG+48%COG(9 台),由5座煤气站进行混气加压。COG 在混合煤气中体积占比与 BFG 相当,但含硫量高,对烟气硫排放的贡献可达70%以上。进一步计算不难得到:若BFG脱硫而COG不脱硫,不能实现烟气SO2超低排放;但当COG硫脱除率达到75%以上,即使BFG不脱硫,也能实现烟气SO2超低排放。因此,决定只对COG精脱硫,经过对各用户COG用气量峰值叠加的概率分析,确定精脱硫的最大处理能力为20万m³/h。
2 主工艺分析及设计
2.1 基本工艺选择
宝钢组织考察和学习了煤气精脱硫的几种技术路线,包括:①微晶吸附法(莱钢),以硅铝酸盐晶体作为分子筛,分级吸附和分离煤气中的杂质;②生化铁—碱溶液催化法脱硫法(DDS 法,南钢),基于传统的 HPF 湿法脱硫工艺,加入亲硫耗氧性耐热耐碱菌及有关催化剂,吸收煤气中的硫分;③加氢转化法(湛钢,用于大制氢系统),有机硫在催化剂的作用下,与煤气中的氢发生转化反应,生成容易被脱除的 H2S ;④水解法(山钢日照,末端使用COG 而非混合煤气),煤气中有机硫(COS、CS2)在催化剂作用下,于合适的温度下 与水蒸气反应,被转化为H2S后继续脱除,即COS+ H2O= H2S +CO2,CS2+2H2O=2H2S +CO2。在综合比较了脱硫效率、总图占地、初始投资、操作条件、运行成本之后,将基本工艺路线锁定在水解法。
2.2 水解法应用概况
20 世纪八九十年代,国内已开始针对合成氨与尿素生产,提出保护工艺催化剂、防止 硫中毒的重要性,在水解法等精脱硫理论和工业应用方面做了大量工作,可使水煤气等煤制合成气中的总硫(主要是H2S 、COS、CS2)≤0.1ppm,并继续向深度净化(总硫≤0.01ppm) 方向进展[1]。在与甲醇联产的煤气化发电系统(IGCC)中,多功能的水解催化剂(主要以铝和钛氧化物为载体)可用于将粗煤气中的COS、CS2水解为易于脱除的H2S,水解转化率在80%以上。近年来,焦炉煤气资源综合利用越来越得到重视,日益广泛地用来制甲醇。但是,由于焦炉煤气本身具有成份复杂且杂质较多的特点,因此制甲醇的关键是焦炉煤气的净化,须采用精脱硫工艺对焦炉气进行进一步脱硫以达到总硫含量≤0.1ppm。很多焦炉气化工企业采用铁钼加氢转化(注:高温高压)有机硫,后串锰铁或氧化锌吸收H2S流程,克服COS水解催化剂对煤气中氧敏感的弱点,但这种流程用于焦炉煤气会出现如原料气中CO 和CO2经过铁钼催化剂发生甲烷化副反应等问题[2]。对此开始有企业应用常温脱硫预处理串中温精脱硫净化工艺,但案例还较为少见。总体来看,水解法的技术原理已较为成熟,有机硫的水解转化可以很彻底,在煤化工行业适用于有机硫含量低但脱硫精度高的场景。
2.3 水解法工艺设计
焦炉煤气与煤制合成气相比,硫、氧、萘、焦油、苯等含量更高,基本工艺条件(操作 压力、温度)存在差异,并且不需要达到 0.1ppm 级高脱硫精度(煤气燃烧后会稀释),因此难以直接移植煤化工行业的脱硫工艺。宝钢结合自身特点进行了适应性优化,以下将介绍主工艺设计的考虑和要点(主工艺流程见图 3)。
图 3 焦炉煤气精脱硫主工艺流程
含硫等主要杂质在工艺流程中的变化如表4所示,其中再生气杂质浓度系指热吹高峰时,H2S 浓度按焦化处理的设计值(非实测值)。另外,COG 含O2约 0.4%,含水近饱和,出入站压力均为6.4kPa。
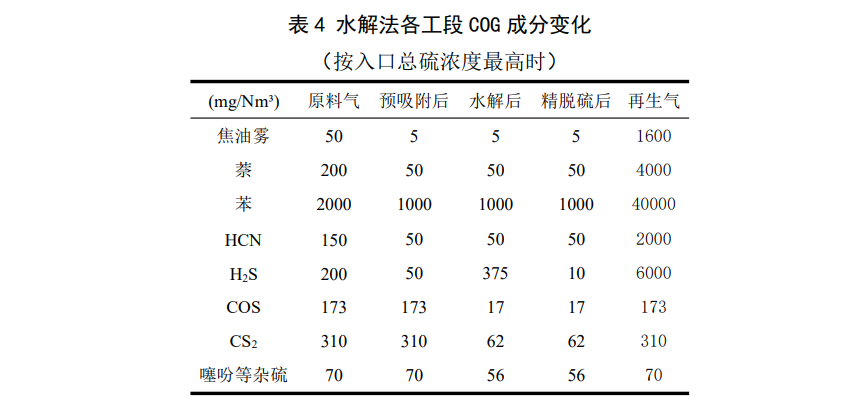
2.3.1 原料气的净化
COG 中的焦油、萘、苯等杂质含量高,若不脱除,会覆盖住催化剂的活性中心和堵塞孔道结构。增加原料气水汽含量有利水解反应向正方向移动,但当原料气水分达到一定程度后,有机硫转化率随水汽含量的增加而下降。H2S也会影响水解催化剂的转化率,这种现象被解释为H2S被氧化后使水解催化剂硫酸盐化中毒而失活[3]。因此,必须对原料气预处理。原料气 COG 首先进入预吸附塔,下进上出。塔内设除油剂(焦炭)及吸附剂(型号B0102+B0103)脱除H2S、萘、苯等杂质及部分水汽,塔底装填白瓷球用作分布气流。使用活性炭吸附主要是一个物理过程,因此当吸附剂床层杂质达到饱和后,可以采用干净气体反吹(上进下出)加热(150~170℃)脱附,之后用常温气体冷吹降温,使塔内填料得以再生。吸附和再生的过程通过程控阀门切换控制,单塔再生时间为 6~7 天。这实际上是气体分离领域常用的变温吸附(TSA)技术的应用。
2.3.2 反吹气的选用
变温吸附一般是以(精脱硫后的)净气加压作为反吹气,以克服塔内床层及至目的地的阻力,这造成投资及运行成本增加,也加大了脱硫装置本身的处理规模。为解决这个问题,工艺设计上采用制氢解吸气作为预吸附塔的反吹气。宝钢厂内有4座制氢站,以PSA工艺变压吸附COG中的氢,制氢尾气及不合格氢气作为解吸气并入煤气柜区的管网。制氢站的原料COG已在冷轧煤气站得到了二次净化——电捕焦及干法脱H2S,并在制氢前的喷水加压和中冷过程进一步洗去了萘。解吸气所含H2S、焦油、萘均只相当于COG的10%,解吸气压力可随管网背压的变化在一定范围内自适应调整,其品质可以满足预吸附塔对反吹气的要求。制氢解吸气流量达1.2~2.0万m³/h,工艺设计上将0.5万m³/h 作为预吸附塔反吹气,其余并入精脱硫系统的原料COG。
2.3.3 再生气的去向
再生气富集了焦油、萘、H2S等杂质,比原料气杂质浓度至少高出1个数量级,若送往拥有源端处理能力的焦化区域,距离过远;若送往炼钢、连铸、烧结区域的小烧嘴用户,极易造成萘结晶堵塞烧嘴和管道。因此,再生气作为“脏气”送往有末端烟气脱硫能力的大流量用户——自备电厂使用。宝钢自备电厂配置了3台350MW的煤气混烧发电机组,主要掺烧BFG;1台350MW和1台150MW的燃气发电机组,主要使用BFG。再生气混入BFG 送往自备电厂可以得到充分的稀释,如图3所示,当BFG 流量为70万m³/h 时,掺混后的煤气含萘28mg/m³,理论上即使在 0℃时仍高于萘的露点;煤气燃烧后烟气SO2浓度约160mg/m³,在发电机组烟气脱硫的能力范围内(~200mg/m³)。
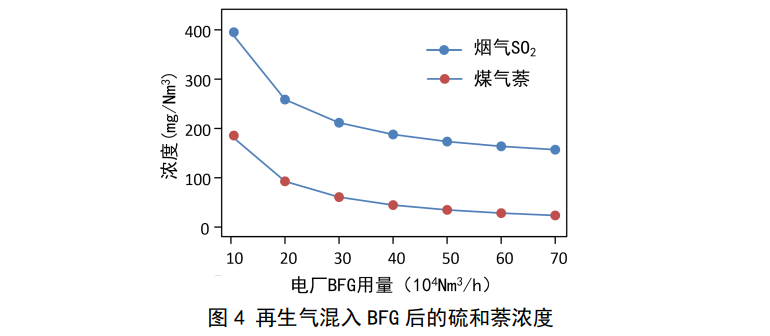
2.3.4 水解过程的分段
多项研究表明,水解催化剂在低温(80℃)条件下就可以对COS 达到较佳的转化效果。CS2催化水解反应则“分步进行”,COS 是水解中间体,即先有 CS2+H2O=COS+H2S,然后 再有 COS+H2O=H2S+CO2。CS2水解在低温下反应能力较弱, 随着温度升高, 水解活性得到极大提高:低于100℃时, CS2水解转化率在5%以下, 提高到130℃, 催化剂水解CS2转化率可达到90%以上[4]。而实际运行中,操作温度降低后将使CS2难以水解转化[5]。基于上述考虑,工艺上对水解过程作分段设计:煤气在第一预热器升温至80~120℃后 进入一级水解塔反应,将COS和部分CS2转化为H2S,这样可避免水解催化剂高温氧中毒, 并有助于降低加热能耗;再经第二预热器继续升温至110~170℃后进入二级水解塔反应,将剩余CS2转化为H2S;若水解催化剂的性能衰减,可调整预热器的温度。相应地,水解催化剂的选用也进行了区分:一级水解塔选用同助系列 TZ-SJ1 型催化剂,主要成分为氧化铝添加特种助剂与稳定剂,以碱金属氧化基载体提升水解剂的抗硫酸盐化能力;二级水解塔选用同助系列 TZ-SJ2 型催化剂,在TZ-SJ1 的基础上添加了贵金属,提升抗高温氧中毒的能力,对 CS2的转化率提高 20%。
2.3.5 硫化氢的吸附
精脱硫工段采用专门针对COG脱硫的KY系列碳基精脱硫剂,具有活性高、稳定性好、 抗杂质气、高硫容的特点,不仅能脱除焦炉气中的H2S,还能脱除部分有机硫。当水解工段的水解剂效率下降时,脱硫剂能对脱有机硫起一定的把关作用。煤气从塔底部进入,通过床层时,借助COG 中的O2将H2S 在低温下选择性氧化生成单质S:2H2S+O2=2S+2H2O。净化气从顶部流出后返回 COG主管网。
2.3.6 原料气的加压
为了将COG从主管网抽取过来、穿过塔器和换热器、将COG再送回主管网,需要对COG 加压并提供15~25kPa 的压头。净气并网压力变化不大,更需要恒流量的加压效果。而罗茨鼓风机为容积式风机,按转速强制输送风量,升压能力高,因此被选用。考虑到来自主管网的COG 依靠自身压力可以穿透预吸附塔,COG 经过净化后有助于缓解杂质对加压机的干扰,预吸附塔和第一预热器之间设置 ZR 系列罗茨鼓风机(工频机与变频机组合)。原料气经加压后会有15℃以上的温升,可以减少水解前的加热量。
2.3.7 物料的换热
换热系统是精脱硫过程必不可少的子系统,来为核心反应装置提供热量或冷量。(1)第一预热器。加压后的25~50℃煤气在第一预热器进行升温至75~120℃,进入第一水解塔反应。热源来自第二水解塔排出的110~170℃的热煤气,进换热器放热后温度降至80~100℃后送至冷却器,通过调节热煤气旁通流量来控制煤气一级预热温度。这种工艺流程避免了蒸汽消耗,体现了温度对口、梯级利用的节能理念。(2)第二预热器。煤气自第一水解塔反应后进入第二预热器,煤气温度从80~120℃继续升温至110~170℃后进入第二水解塔。热源为中压蒸汽(3.2~3.8MPa,温度260℃),通过蒸汽流量调节阀来控制出口煤气温度。(3)冷却器。由于第二水解塔后的煤气经第一级预热器放热后还有80~100℃,温度较高,不能直接进煤气管网和精脱硫塔(低温吸附H2S),为此设置煤气冷却器,将煤气出口温度降至45℃以下。冷却器水侧采用循环冷却水。(4)再生气加热器。预吸附塔再生时热吹温度为150~170℃,气源采用常温的制氢解吸气,热源为中压蒸汽及低压闪蒸蒸汽,通过蒸汽流量调节阀来控制出口煤气温度。(5)疏水闪蒸及冷凝水回收装置。以闪蒸罐收集第二预热器和再生气加热器的中压蒸汽疏水,将闪蒸汽送到再生加热器利用。闪蒸罐体水位达高位时,可排水至冷凝水箱。冷凝水箱还收集再生气加热器的低压蒸汽疏水,以泵压送至附近的锅炉补水箱和中水场。
2.3.8 废弃物的不出厂处理
预吸附塔产生的废吸附剂(活性炭和焦炭为主)、精脱硫塔产生的废脱硫剂(活性炭为主)属于危险废物。活性炭和焦炭可送至烧结单元,与烧结用粗焦混合后燃烧。经测算,烧结烟气中SO2浓度增加约30mg/m³,其烟气脱硫装置可以消纳。水解塔产生的废催化剂(金属氧化物)属于一般工业固废。由于其中铝、钛、钾、硅元素含量过高,烧结单元无法接纳处理,只能送去焚烧炉。水解催化剂基本不含硫、重金属,满足焚烧炉入炉要求,因此可以送至焚烧炉处理。液体废弃物为焦炉煤气冷凝液,该冷凝液主要含有焦油、萘,集中排放到附近的酚水坑中,由槽车定期抽送至焦化处理后再利用。
3 精脱硫与煤气管网的连结
3.1 连结位置的选择
如图 5 所示,宝钢焦炉煤气管网在以水封阀组控制气流走向后具有以下特点[6]:供往轧钢5座煤气站的COG都可以经过CW004水封阀,“守住”CW004 就可以控制COG品质, 这就是COG总管精脱硫的概念。水解法的主工艺设计基本解决了精脱硫的“热力-化学反应 过程”,而这么一套庞大的工艺单元如何“连结”到原有系统,就是煤气管网的“动力过程”需要解决的问题。选址总管脱硫将存在精脱硫系统加压过程与轧钢5个煤气混合加压相互干扰的问题。对此,将精脱硫出口管道与COG 柜相连,以煤气柜捕捉管网压力的变动情况进行压力自平衡,煤气柜的活塞配重即为精脱硫系统出口运行压力,精脱硫出口煤气量和使用量间的波动由煤气柜吐纳吸收,也为减少精脱硫装置罗茨风机频繁的变负荷调节创造条件。
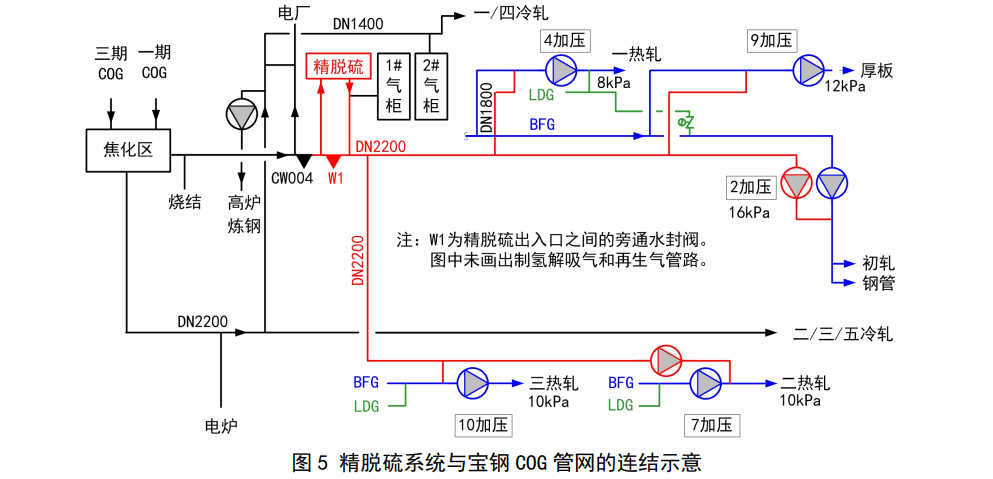
3.2 与煤气柜的联网
精脱硫后净气与原有系统的连接形成的最简单模式如图6所示。Q1为COG 送轧钢加热炉的流量,Q2为精脱硫净气出口流量,Q3为精脱硫旁通水封的COG 流量(具有方向性)。煤气柜的入口与其它用户主管通流,精脱硫出入口之间的旁通水封阀打开,净气与煤气柜之间不流通,Q1=Q2+Q3。当 Q2>Q1时Q3<0,部分净气会向气源侧和其它用户流动;当Q2<Q1时Q3>0,部分原料气会经过旁通水封向轧钢方向流动。这种模式下,精脱硫的加压机适合定流量运行,即罗茨机保持固定转速或频率,控制净化气量大于轧钢用COG 量,就可以保证轧钢方向一直使用净气。但要牺牲一定的经济性, 即造成精脱硫系统“过量”运行,使得部分净气未对口使用而供往了其它用户。
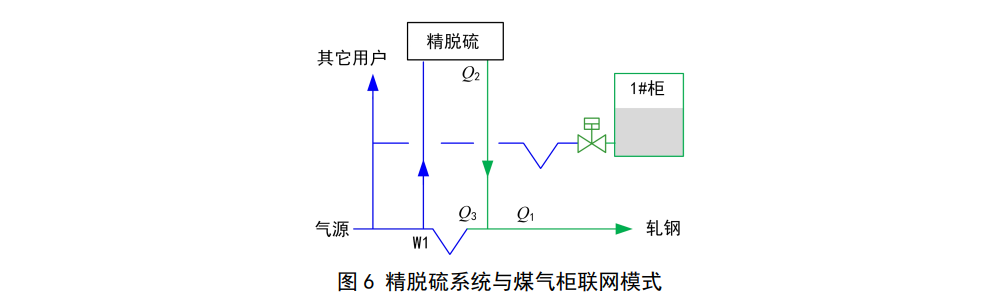
3.3 控制系统的连结
控制系统构成包括两套:由DCS 实现精脱硫主系统全流程的数据采集、过程监控;在能源中心EMS计算机监控系统新增I/O服务器,通过OPC-UA 通讯方式与DCS 实时通讯, 结合EMS系统已有的煤气柜、煤气管网、环保烟气排口等信息,按现场无人值守模式,对精脱硫系统及煤气管网实施一体化的监控。
4 实施及初步效果
4.1 工程化实施
“宝山基地焦炉煤气精脱硫改造”技改项目,按处理气量20万m³/h、COG 入口总硫900mg/m³(以SO2计)、出口总硫≤190mg/m³(以SO2计)、COS 脱除率≥90%,CS2脱除率 ≥80%设计。主要能源消耗为蒸汽7t/h、电力 1800万kWh/a,设计煤气运营成本约0.05元/m³(包括填料及更换费用等)。项目主要设备见表7。
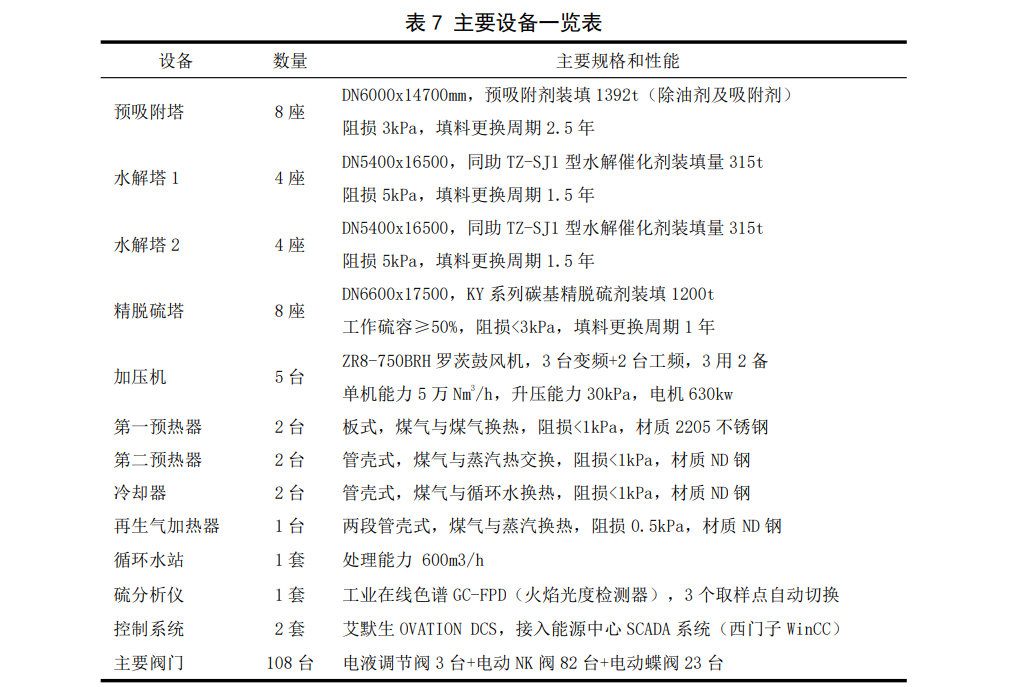
原料气取自COG总管(DN2200),脱硫后的焦炉煤气回送管网,同时增设稳压管和阀门与2座COG柜之间的DN2000联络管相连。脱硫装置主体设施布置在高焦煤气柜区,电气室、循环水站等辅助设施就近布置,建设用地8160㎡。项目主体部分从2021年11月13日开始打桩、春节后进入设备安装阶段,先后完成了复杂的焦炉煤气主管网接口,克服了时间紧(因疫情停工3.5 个月)、场地受限、钢结构施工量大的困难,于2022年9月30日进入试运行阶段。
4.2 运行效果
(1)考虑到水解剂活性会逐渐降低,初期运行时水解反应温度暂设置在最低限。表8为精脱硫系统投运后代表性工况下的各节点硫含量的人工取样色谱分析结果。
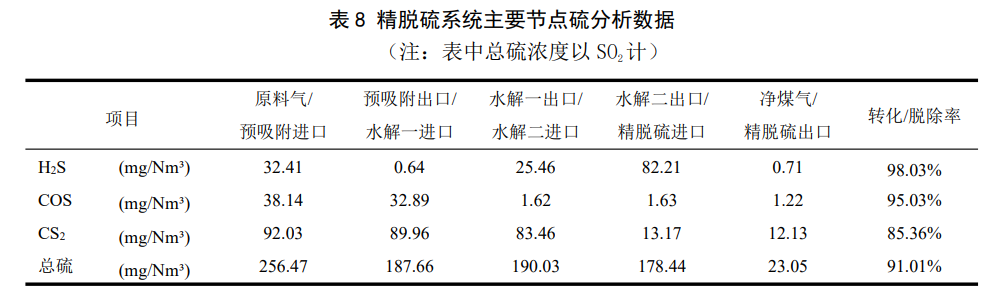
从数据可以看出:预吸附塔对H2S具有较强的脱除率(排污液几乎不含S元素、绝大部分被再生气带向电厂);COS 在水解一段中已得到较好的转化;CS2确实与反应温度正相 关——在水解一段中仅少量脱除,主要在水解二段中被转化。系统对有机硫的转化率保持在85%以上,总硫脱除率在90%以上。
(2)轧钢加热炉各烟气排口的SO2浓度显著下降,平均下降了50%以上,如图6示例。项目帮助宝钢继续完成了全厂62%的COG 硫污染治理,并达到超低排放标准。
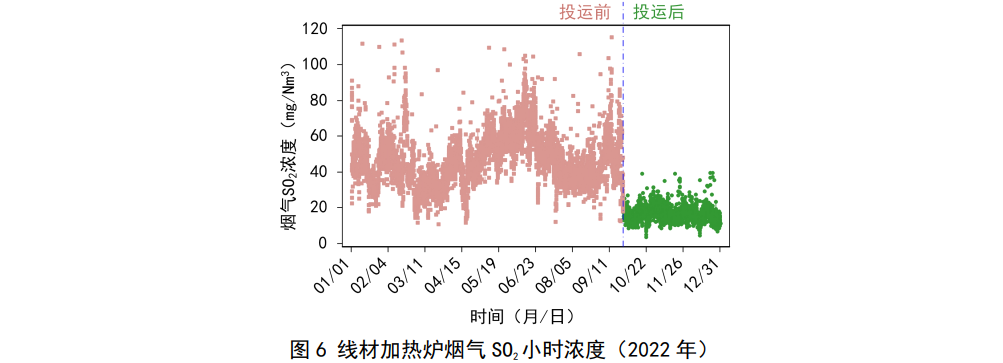
(3)因采用了与煤气柜联网等一系列措施使精脱硫系统能够稳定运行,日常工况调整,甚至精脱硫因外部管道缺陷而停运2次,用户都无感知。由于预吸附塔、复合塔保温和储热性能较好,即使精脱硫系统停运10小时,也能在复役后数小时内再次达到脱硫效果。
(4)从运行情况反观设计阶段,最大的问题是未曾设想到预吸附塔的排液问题:热吹时焦油、萘等大量析出,其混合体很难被再生气带走,极易堵塞排污管路。好在已经形成对策和改进措施,堵塞问题正得到解决。
5 结语
钢铁企业广泛地以混合煤气作为燃料,而通过何种煤气精脱硫实现超低排放,需要根据燃料结构、硫平衡分析等因厂制宜地确定方向。在具体技术路线上,煤化工行业的水解法值得钢铁行业学习和借鉴,在此基础上应结合煤气管网设施作适应性优化。对宝钢而言,虽然焦炉煤气精脱硫取得了初步效果,但COS 和CS2等有机硫组分的水解转化保持长期稳定将是今后燃气专业的重点课题。
作者:邓万里 1,李霁 1 ,杨静 2(1.宝山钢铁股份有限公司能源环保部;2.宝钢工程技术集团有限公司)